ABOUT CERAMIC COMPOSITE RESISTORS
Ceramic composition resistors have long been recognized for their advantages in pulsed duty, requiring combinations of high peak power or high voltage with low inductance. This is why they are the best choice for snubbers and inrush limiting applications.
The simple construction consists of a sintered ceramic and conductive particles dispersed throughout the element body, metal contacts on the ends of the body, and depending on the application an anti-track or UL rated epoxy coating. The resistive ceramic element is manufactured using a specific mixture of clays, alumina, and carbon.
Selection of the proper material resistivities of the ceramic mix from among several options allows the properties to be controlled and tailored to the application. Once mixed, the material is granulated and pressed into the specific shape needed, with diameters ranging from 3 to 152mm. This pressed mixture is then fired in a tunnel kiln with a precisely controlled reducing atmosphere. This produces a high-temperature and electrically conductive bulk ceramic composite resistor.
To produce the electrical contacts, aluminum, copper, or brass is flame sprayed onto the flat surfaces. In the case where connections are soldered to the metallization, the further addition of Sn, Zn, PD, Cu, Ag, Zr, and Co creates a metal surface that is electrically conductive and mechanically highly reliable.
For Discs, Rods, and Tubes an anti-track coating is applied to the edges to improve dielectric withstand. In the case of PCB mount parts, a solvent-resistant epoxy coating is used, allowing for operation in almost any environment.
A wide variety of geometries and a range of resistivity are able to handle hundreds of Joules to Mega Joules of energy. These ceramic composition resistors are robust, having a constant mechanical strength, allowing for good compression specifications and the ability to absorb transmitted mechanical shock, as long as the direct impact is avoided.
Technical Advantage
Ceramic composite linear resistors are ideal for applications that require a component to operate at high voltage, provide high energy absorption, and be non-inductive.
Compared to film or wire wound resistors where the resistive element is only a small fraction of the total mass of the component, bulk construction concentrates most of the component mass into the resistive element allowing high energy events to be uniformly distributed through the entire ceramic composite material, there is no film or wire to fail. This bestows the capacity for high peak power and high reliability in pulsed or surge-prone duty. Because 100% of the active material is conductive, it produces a resistor with minimum size for pulse or high energy applications. Bulk resistors are inherently non-inductive, and offer high energy density.
Compared to carbon composite resistors, ceramic composite resistors dissipate heat more rapidly, so a higher average power can be tolerated. The high-temperature capability of the ceramic also allows much more energy density than carbon composition resistors, which means smaller or fewer parts, resulting in better reliability and lowered cost. Ceramic resistors also exhibit better stability under extreme voltage and temperature. Like other "bulk" resistors, they are non-inductive. This makes them ideal for high-frequency applications.
Ceramic Composition Resistors are ideal for Under-Oil use
Most resistive elements are not well suited for the combination of high voltage and high energy. When traditional resistive elements (wound or film type) are used under oil, high energies events result in large temperature rises in the conductive element. This high heat flux is difficult to dissipate due to the low surface area of the element. The high heat produced in these small elements also introduces the risk of oil degradation. In the case of Biodegradable oils, which are becoming more common place, they have higher moisture and can have more hydrocarbon gas dissolved in the oil. This can result in oil degradation affecting key thermal and electrical specifications.
Ceramic Composition resistors have a much lower temperature rise for a given high-energy event, since 100% of the active material is conductive it allows energy and power to be uniformly distributed through the entire ceramic. The element also has a much larger surface area allowing thermal energy to be more readily conducted into the oil. Performance under most oils is also well known.
Applications
When used in applications where the non-inductive, high voltage and energy capability are needed, ceramic composite resistors tend to be smaller, and lighter than traditional wound components. These are ideal for applications such as:
- Capacitor Charge and Discharge
- Crowbar
- Electrical Transmission
- High Voltage Power Supply
- AC/DC Motor Drives
- Dynamic Braking Systems
- High Voltage Pulse Generator
- X-Ray Equipment
- EMF / RFI Test Circuits
- RC Snubber Circuits
- RF Power Amplifiers
- Plasma Generator
- High-Voltage Circuits
PCB MOUNT LOW VOLTAGE CERAMIC COMPOSITION RESISTORS
There are three series of PCB Mount Low Voltage Ceramic Composite Resistors. The overall construction of these resistors is the same; the main difference is the physical size and energy rating of the parts.
U-Series
These are PCB mount compact ceramic composite resistors offered in a surge energy rating from 250 Joules to 2800 Joules. They come in a low-cost, epoxy-coated, radial leaded form factor. The U-Series is designed to provide an optimum solution to many Power Electronics applications; which include DC Charging Stations, Energy Storage Inverters, Welders, High-frequency DC/DC converter, Adjustable Speed Drive (ASDs), Charging Inverters, Wireless High Frequency Charging, Traction Inverters, High-Performance Hybrid Electric Vehicles (HEVs) and RF Power Amplifiers.
Other circuit applications are also suited such as surge limiting and pulse shaping. Because they are inherently non-inductive and have the ability to withstand transient high voltage impulses, they are also appropriate for over-voltage protection and crowbar capacitor charge / discharge applications. In pulsed applications, these compact resistors distribute the energy uniformly throughout their structure, resulting in low thermal stress. The consequences are increased reliability and reduced size compared to other resistor types. High-temperature, solvent-resistant epoxy coating allows operation in almost any environment.
The U- Series of high energy surge resistors use the same process as our other ceramic resistors using a specific mixture of clays, alumina, and carbon. Once mixed, the material is granulated and pressed into a specific shape needed. This pressed mixture is then fired in a tunnel kiln with a precisely controlled reducing atmosphere. This produces a bulk ceramic carbon resistor which is 100% active material, and therefore of minimum size providing a non-inductive resistor with a high surge energy rating ideal for Power Electronics applications such as:
- Energy Storage Inverters
- DC Charging Stations
- Welders
- High-frequency DC/DC converter
- Adjustable Speed Drive (ASDs)
- High Voltage Power Supply
- Wireless High Frequency Charging
- Traction Inverters
- High-Performance Hybrid Electric Vehicles (HEVs)
- RF Power Amplifiers
Specifications for U-Series ceramic resistors
RT-Series
These are PCB mount bulk ceramic resistors that are compact and non-inductive, ideal for circuitry associated with surges, high peak power, or high energy. They are offered in a surge energy rating of 70 Joules and frequently replace multi-watt carbon composition resistors which just provide a passable solution at low average power. Carbon composition resistors also can develop stability issues as a result of moisture or high voltage and can be difficult to source or are obsolete.
RT-Series bulk ceramic resistors do not have these limitations, providing superior performance in high voltage power supplies, R-C snubber circuits, and inrush limiters. For pulsed applications, these compact non-inductive resistors distribute the energy uniformly throughout their structure, resulting in low thermal stress. The consequence is increased reliability, and in many cases, reduced size, compared to wire-wound or film types. The solvent-resistant epoxy coating allows operation in almost any environment without the moisture absorption concerns of carbon composition resistors.
These high surge energy resistors use the same process as our other ceramic resistors using a specific mixture of clays, alumina, and carbon. Once mixed, the material is granulated and pressed into a specific shape needed. This pressed mixture is then fired in a tunnel kiln with a precisely controlled reducing atmosphere. This produces a bulk ceramic carbon resistor which is 100% active material, and therefore of minimum size.
The 100% active material of the RT-Series results in compact size providing a non-inductive resistor with a high surge energy rating ideal for Power Electronics applications such as:
- High-frequency DC/DC converter
- Welders
- DC Charging Stations
- High-Performance Hybrid Electric Vehicles (HEVs)
- Adjustable Speed Drive (ASDs)
- RF Power Amplifiers
- Charging Inverters
- High Voltage Power Supply
- Traction Inverters
Specifications for RT-Series ceramic resistors
SR-Series
This PCB-mounted series of surge resistors are capable of handling surge energies from 250 to 10,400 Joules. As with our other ceramic resistors, these are manufactured from a carefully selected mixture of clays, alumina, and carbon. This mixture is blended, pressed into the required shape, and then fired in a controlled atmosphere at high temperatures. The end contacts are constructed with gold-plated brass terminations attached to copper metalized contacts on opposing flat surfaces of the resistor body, with a high melting point solder. Short-term operation is possible at temperatures up to 200 °C.
The resistor has a UL94 V-0-approved epoxy resin coating applied by using a fluidized bed. This coating has a hard, smooth finish, providing enhanced dielectric withstand and mechanical robustness. This coating also maintains the aesthetics of your PCB assembly it looks similar to other electronic components. Note, if the surface temperature repeatedly exceeds 150 °C, the coating will become slightly degraded and the color will turn darker. This discoloration does not indicate that its performance is compromised. Also, while this coating can diminish the rate of moisture ingress, it is not impervious to liquids.
The gold-plated brass spring termination pins are 1.5mm wide by 0.4mm thick with the spring pin format designed to ensure stability during PCB assembly. We recommend minimum PCB mounting holes of 2.0mm in diameter. If soldering, use mildly activated fluxed solders with liquidous properties less than 230 °C.
The 100% active material of the SR-Series results in compact size providing a non-inductive resistor with a high surge energy rating ideal for Power Electronics applications such as:
- DC Charging Stations
- Welders
- Wireless High Frequency Charging
- Charging Inverters
- Energy Storage Inverters
- Current Limiting Resistor
- High-Performance Hybrid Electric Vehicles (HEVs)
- Adjustable Speed Drive (ASDs)
- RF Power Amplifiers
- High Voltage Pulse Generator
- High-frequency DC/DC converter
- Traction Inverters
Specifications for SR-Series ceramic resistors
PCB MOUNT HIGH VOLTAGE RESISTORS
C-Series
These PCB mount resistors are rated for extremely high voltage given their compact size and are offered in a surge energy rating from 100 to 5600 Joules. As with other ceramic resistors they are non-inductive, but these radial leaded resistors can absorb high energy at voltages up to 44kV. A special high voltage epoxy coating allows for circuit board mounting, making them ideal for high voltage resistor applications requiring non-inductance, as in pulse forming and fast crowbars.
The C- Series of high voltage resistors uses the same process as our other ceramic resistors using a specific mixture of clays, alumina, and carbon. Once mixed the material is granulated and pressed into a specific shape needed. This pressed mixture is then fired in a tunnel kiln with a precisely controlled reducing atmosphere.
They are now available with gold-plated lead wires, which are solderable per J-STD-002C and offer improved solderability as opposed to tin-plated leads.
This produces a bulk ceramic carbon resistor that has 100% active material, with minimum size, non-inductive, and a high voltage epoxy coating. These are commonly used as a high voltage pulse shaping resistor or protection against surge voltages. Ideal applications include:
- High Voltage Pulse Generator
- X-ray Power Supplies
- Current Limiting Resistor
- High Voltage Resistor
- Fast Crowbars
- High Voltage Power Supply
- Automated External Defibrillators (AEDs)
- High Voltage Test Equipment
- Plasma Generator
Specifications for C-Series ceramic resistors
ROD & TUBE RESISTORS
Rod and Tube style ceramic resistors, as with our other ceramic resistors, are manufactured from a carefully selected mixture of clays, alumina, and carbon. This mixture is blended, extruded into the required shape, and then fired at high temperatures in a controlled atmosphere. Electrical contacts are made by flame-spraying aluminum onto the end surfaces. Other metallization’s are available.
The standard termination is a spring clip connecting to the metalized ferrule ends. Alternatives such as radial tabs and high voltage corona shielded terminals, allow for mounting options to enhance performance. Optional coatings are available to optimize performance in air, oil, or other dielectrics.
Rod and Tube high power resistors are used in circuits requiring high voltage and non-inductance with surge energy. These have surge energy ratings ranging from 1000 to 140,000 Joules The tube configuration provides more effective convection cooling allowing a higher average power rating of up to 300 Watts. Resistors are available with outside diameters ranging from 10mm to 50mm and in lengths up to 600mm.
We have direct crosses to Kanthal® Globar® - Tubular Resistors - Series 800 and 1000 - AS Material Type - Carbon Ceramic and SP Material Type - Silicon Glass.
These resistors are suited as the anti-parasitic elements in the grid anode circuits of induction heaters and RC snubbers for MVA dry-type transformers. Other ideal applications include:
- High-Voltage Circuits
- Impulse Generators
- Current Limiting Resistors
- Electrical Transmission
- X-Ray Equipment
- Overvoltage Protection
- High Voltage Power Supplies
- Capacitor Charge/Discharge
- Laser/Imaging equipment
- RF Combiners
- High Voltage Pulse Generator
- Oscillatory De-Qing Circuits
Specifications for ceramic Rods & Tube resistors
HIGH ENERGY DISK RESISTORS
High energy ceramic disk resistors provide unequaled performance in high energy and high voltage applications, up to 110kJ per disc. As with our other ceramic resistors, these are manufactured from a carefully selected mixture of clays, alumina, and carbon.
This mixture is blended, pressed into the required shape, and then fired in a tunnel kiln in a controlled atmosphere at high temperatures. This produces a bulk ceramic resistor which is 100% active material, and therefore of minimum size. Electrical contacts are made by flame spraying aluminum onto the end surfaces. Other metallization’s are available.
These non-inductive, bulk ceramic resistors are designed for pulse shaping, crowbar, and capacitor charge/discharge. The disks can handle hundreds of kJ per disc or be configured into Mega-Joule assemblies which are also suited for high voltage applications Disk resistors can be heat sink mounted for high average power requirements.
These high power resistors distribute energy uniformly throughout their structure for low thermal stress. The standard, high-temperature silicone coating enhances high voltage performance in air. Optional configurations optimize performance in other gaseous or fluid dielectrics. Pulsed power systems are ideal applications.
Specifications for High Energy Ceramic Disc Resistors
HIGH ENERGY DISK ASSEMBLIES
High power resistor assemblies integrate multiple ceramic resistor elements to meet especially challenging requirements with an economic and flexible solution.
Disks can be assembled into high power resistor assemblies which are able to handle energies to megajoules, average energy to hundreds of kilowatts, and voltage to hundreds of kilovolts.
Using stock and pre-engineered components, we can provide a packaged economical solution to your demanding resistor applications for voltage clamping, capacitor charge and dump, high power snubbers, and high voltage pulsed power. Other applications are for high-protection resistor surge voltages. Assembled voltage and energy surge ratings are the sum of the individual disk ratings.
Bulk ceramic resistors can be offered separately, in matched sets, or ready-assembled high-power resistors for ease of installation, depending on the application.
Standard ceramic resistor assemblies include the following components:
- Glass fiber tie rod for disk mounting
- Aluminum hexagon end stops, pinned at either end
- Belleville or coned-disc springs to provide compressive mounting force
- Insulated stand offs, Glastic®
- Aluminum terminals for electrical contact
- Mounting using GPO-3 or G-10 type materials
High Voltage Stacked Disk Assemblies - I-Series
High voltage or energy applications which experience surge events in the range of tens of kilojoules at low average power are suited for stacked disk assemblies with ferrule-ends. Up to twenty 32mm or 50mm disk resistors are integrated in series to create a single, dependable and economical component.
Ferrule terminations in various styles provide a contour suitable for high voltage, interfacing easily into our high voltage endcaps for termination and mounting. Assemblies for use under oil are also available with disks pre-impregnated or designed for oil immersion.
High Energy Stacked Disk Assemblies - J-Series
For high energy events, these stacked resistor assemblies use heavy-duty components for mechanical mounting, electrical isolation, and termination. Up to twenty-five of 75mm, 112mm, or 152mm disk resistors are combined in series, providing ratings to thousands of kilojoules to megajoules in a single-surge energy event.
Termination options include a tab, cable, or bus bar interface. Coating options optimize performance in air, liquid, or gas dielectric. Assemblies for use under oil are also available with disks pre-impregnated or designed for oil immersion.
Convection Cooled High Energy/Power Stacked Disk Assemblies -K-Series
Aluminum or other metal cooling fins are integrated into our high energy stacked disk assemblies, to create a resistor assembly with improved forced or free-air convection cooling.
This increases the average power rating while maintaining its high surge energy capability. When the resistor sees repetitive surge events, this assembly method will reduce cool-down time important in crowbar or energy dump applications.
Liquid-Cooled High Energy/Power Stacked Disk Assemblies -H-Series
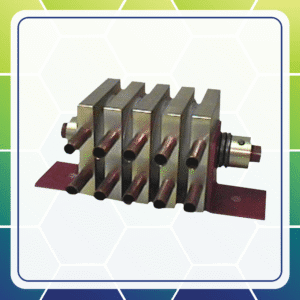
Using liquid-cooled plates for increased average power rating, this series achieves surge duty at very high average power. Cooling plates can be electrically isolated from the resistor disk, simplifying your product assembly by sharing the same cooling path used by other power electronic components. Separate heat exchangers are not needed.
Other special techniques and materials are used for disk-to-heatsink interfaces to achieve high power density at a low cost per kilowatt. The power density of 500 watts to 3kW per disk, along with arrays configured in series/parallel arrangements are able to handle hundreds of kilowatts of continuous power.
EARTHING STICKS
Earthing Sticks are used specifically for high-voltage, high-energy discharge applications where operator safety is the prime concern. These consist of an integrated array of high-energy ceramic disk resistors, providing a secure and reliable means to discharge potentially lethal energy from high-voltage equipment.
The Earthing Sticks come with an ergonomically designed handle and protection shield integrated into them. A permanent earth connection is maintained
using the earth hook and high-voltage cable, allowing stored energy to be safely discharged into the ceramic resistor disks.
These Ground Sticks are custom configured to your application with disk diameters from 32mm - 75mm. Disk size and quantity used is dependent on voltage and energy levels. In general Earthing Sticks should limit discharge current to a maximum of 50 amps. Voltage ratings exceeding 100kv and energy dissipation exceeding 100kj are possible. If needed hard ground sticks without discharge resistors are available which can include: stainless steel Hook probe, Handgrip, Safety blast shield, and High-Voltage HiFlex ground cable with a ring terminal.
Earthing Stick Capabilities
- Non-Inductive
- Discharge potentially lethal energy
- Voltage ratings exceeding 100kV
- Energy dissipation exceeding 100kJ